We are always thinking one step aheadConsulting, Engineering & Optimization in Logistics Networks
How can we help you?
Smit & zoon increases its effectiveness by outsourcing its logistics
Interview with René Weltevrede, Operational Director, and Arnaud Backbier, Supply Chain Manager, from Smit & zoon by Marcel te Lindert
Smit & zoon has two production facilities located 40 kilometers apart – one in Weesp and the other
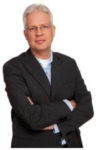
in Amersfoort. The family-run company, which has been around for almost 200 years, develops and manufactures leather chemicals for use by tanneries. Fish oil is often the primary raw material in its products. The Weesp facility also houses the business unit that sources, processes and sells food-quality and feed-quality fish oil that is used as an ingredient in food products and animal feed, among other things. Because many customers order products from both facilities, up until recently there was a lot of transport activity backwards and forwards between Weesp and Amersfoort, with trucks having to collect goods from both sites. “From a logistics perspective that was definitely not the ideal solution,” confirms René Weltevrede, Operational Director at Smit & zoon.
Smit & zoon has two production facilities located 40 kilometers apart – one in Weesp and the other in Amersfoort. The family-run company, which has been around for almost 200 years, develops and manufactures leather chemicals for use by tanneries. Fish oil is often the primary raw material in its products. The Weesp facility also houses the business unit that sources, processes and sells food-quality and feed-quality fish oil that is used as an ingredient in food products and animal feed, among other things. Because many customers order products from both facilities, up until recently there was a lot of transport activity backwards and forwards between Weesp and Amersfoort, with trucks having to collect goods from both sites. “From a logistics perspective that was definitely not the ideal solution,” confirms René Weltevrede, Operational Director at Smit & zoon.
An even more pressing issue was the lack of space at both of the Smit & zoon sites. In Amersfoort, Weltevrede had to hire external warehousing space to store some of the 2,000 tons’ worth of pallets stacked with bagged products. In Weesp, meanwhile, the outdoor storage area had become too small to hold the company’s 1,400 tons of chemicals, mainly fatliquors, stored in drums and IBCs. “That meant numerous forklift maneuvers to retrieve the right products from storage. Plus the outdoor storage situation was no longer sustainable. Not only did we run the risk of our products freezing in the winter, but we were also keen to put an end to them getting so dirty due to rain, leaves and bird droppings.”
Preference for outsourcing
Smit & zoon decided to enlist Groenewout’s help to conduct a feasibility study which would explore the various options and their financial implications. Would it make sense for the company to build its own new central warehouse or would it be better to outsource the operations to a logistics service provider? “Groenewout gathered together all the data and then investigated the various goods flows to identify the center of gravity,” explains Weltevrede.
The conclusion was that outsourcing would be preferable to going it alone. “It was definitely not an option to build a new warehouse on our own premises because we simply didn’t have enough room,” comments Weltevrede.
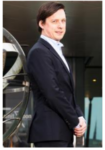
His colleague Arnaud Backbier, Supply Chain Manager at Smit & zoon, adds: “In addition, the analysis revealed that the center of gravity was close to Rotterdam, which is not surprising seeing as particularly the leather chemicals are mainly exported overseas and two thirds of our goods leave the country via the Port of Rotterdam. Having a warehouse in that area means that we now have to deliver all our stock to that location. But the advantages are that we no longer transport half-empty loads between Weesp and Amersfoort and that we can offer our customers shorter delivery times.”
Tender procedure
Groenewout was also asked to coordinate the subsequent project: selecting the logistics service provider. The consultancy firm assisted in the tender procedure and in evaluating the proposals and even accompanied Smit & zoon on visits to companies given as references.
Neele-Vat Logistics was ultimately chosen due mainly, according to Weltevrede, to the supplier’s professionalism and quality level. “This logistics service provider has a very robust internal organization for implementing processes like this. They understand not only the physical flows of goods but also the flows of information that are extremely important to our operational success. That IT aspect is pretty complex in our case and Neele-Vat Logistics has a lot of relevant experience, plus they have an excellent location in the Maasvlakte development. Our products can be at the terminal within just 15 minutes.”
Off to a quick start
Smit & zoon divided the operational implementation into two phases. The first phase entailed moving the inventory to the Maasvlakte development, where Neele-Vat Logistics got off to a quick start with limited IT support. “We could choose between waiting for a long time until the complete EDI message traffic between our facilities and the warehouse was fully implemented, or to get things underway quickly with a limited set of messages and extra manual work. We decided on the second option because of the lack of space, especially in Weesp – it was becoming a real squeeze there,” explains Weltevrede.
Once the first phase was complete, Smit & zoon took the time to reflect on the experience and the lessons learned. Outsourcing was more complicated than they had expected, says Backbier.
“The complexity is primarily due to the large number of different labels our products are traded under. During the order picking process, Neele-Vat Logistics has to retrieve the right quantities of the right types of drums and IBCs containing the relevant chemicals from the storage locations and label them correctly. In hindsight, that was too complex to automate which resulted in a number of errors. That’s why, in the second phase, we decided to label all the chemicals on site in Weesp before sending them to the Maasvlakte facility. At the same time we initiated a project to reduce the number of label variations so that we don’t have to keep so much stock in the warehouse.”
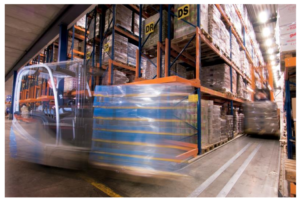
Increased costs
Even though the second phase presented a few challenges, at Smit & zoon they regard it as a successful project. “We’ve achieved our objectives: our products are no longer stored outdoors, for example. We’ve resolved the space shortage in Weesp which has reduced the stress and improved safety again. And in Amersfoort we no longer need to hire external warehousing,” continues Backbier, summing up the outcomes. And yet the operation has not resulted in lower costs. “But that’s not really surprising because we now have a warehouse which we didn’t have before so it’s only logical that the costs will increase. An added advantage of outsourcing is that it gives us more insight into those costs, which often remained hidden in the past. We can now see precisely how much it costs us to introduce a new label. That helps us to make the right decisions in that respect,” states Weltevrede.
The total project has had a big impact on the organization: “Not only in relation to the labels, but also in terms of our planning. In Weesp, we’ve switched from make-to-order to make-to-stock.
That’s a major transition, not least because our employees in Weesp no longer see any stock. There aren’t any stacks of drums and IBCs on site any more – just numbers on a computer screen showing how much stock we have. That will take some getting used to so we’ve still got some way to go, especially in terms of inventory management.”
Rapid results
In addition to the feasibility study and the tender procedure, Groenewout also coordinated the process implementation at Neele-Vat Logistics. “We were assigned an experienced consultant with an understanding of both logistics and ICT plus with the necessary project management skills. That worked extremely well,” says Weltevrede, before adding that the company’s relationship with Groenewout dates back to more than a decade ago. “So when we were looking for a consultancy firm, that long-standing relationship meant that it didn’t take us long to decide on Groenewout again. And they’ve shown we were right to place our trust in them. The Groenewout consultants understand how our organization works and proactively get involved – plus they deliver rapid results, as we saw during the feasibility study.”
Weltevrede is referring to the large database containing cost components that enables Groenewout to calculate the effects of the various options quickly and efficiently. “Of course, as the client we had to stay alert but that was also our role in the process. On a project like this, you have to work together.”
Text by Marcel te Lindert
Marcel te Lindert is a journalist with over 20 years of experience in logistics. He was editor-in-chief of the Dutch magazines Transport+Opslag and Logistiek. Nowadays he works freelance for trade magazines including Supply Chain Magazine and Logistiek Totaal.
More information
If you would like more information about this project, please contact Groenewout or call tel. +31 (0)76 533 04 40. Further information about Smit & zoon, please go to www.smitzoon.com.