We are always thinking one step aheadConsulting, Engineering & Optimization in Logistics Networks
How can we help you?
New fulfillment center puts Restocks on a firm footing
Interview with Jay Lopes, Head of Operations at Restocks
The business started small, based on a love and passion for sneakers, in rented office space in the Dutch town of Barendrecht. “Day in, day out, for eight months solid, we worked on developing the platform – because fundamentally we’re a tech company,” says Jay Lopes, Head of Operations at Restocks. “Our platform is the beating heart of the company. It bridges the gap between buyers and sellers of limited-edition sneakers.”

Restocks went live in 2019. The company enjoyed immediate success, benefitting from the e-commerce boom, and the annual growth rate climbed to unprecedented levels of as much as 400%, especially during the COVID-19 pandemic. “We spotted a gap in the European market and caught the wave at the right time,” says Lopes. “That’s great, but you have to be ready for that.
There’s a good reason that we put so much time and energy into developing our platform in the early months. It had to be flexible and scalable. We need to be able to handle 2,000 orders a day just as capably as 500 orders a day.”
New business model
Besides investing in the flexible and scalable platform, Restocks also invested in process efficiency. “We consciously combined tech and logistics wherever possible and automated lots of things,” explains Lopes. That certainly paid off for the startup, because Restocks is now the European market leader. The platform remains the beating heart of the company, but the activities have been expanded. For example, a new business model was introduced in 2020 which resulted in more process complexity. Lopes: “That’s when we launched our consignment model. In other words, we hold stock for resellers who want us to. For that, you need extra storage space and the right storage systems, plus your picking and packing processes need to be set up efficiently.”
Separating the operations
The stock levels went through the roof (almost literally!). From initially holding just a few dozen items in stock, Restocks saw its inventory rise to 10,000 items. The company relocated three times within Barendrecht, until finally deciding to move to the city of Breda in late 2020. The new location offered space for 26,000 items, but even that became a tight squeeze after just two months.
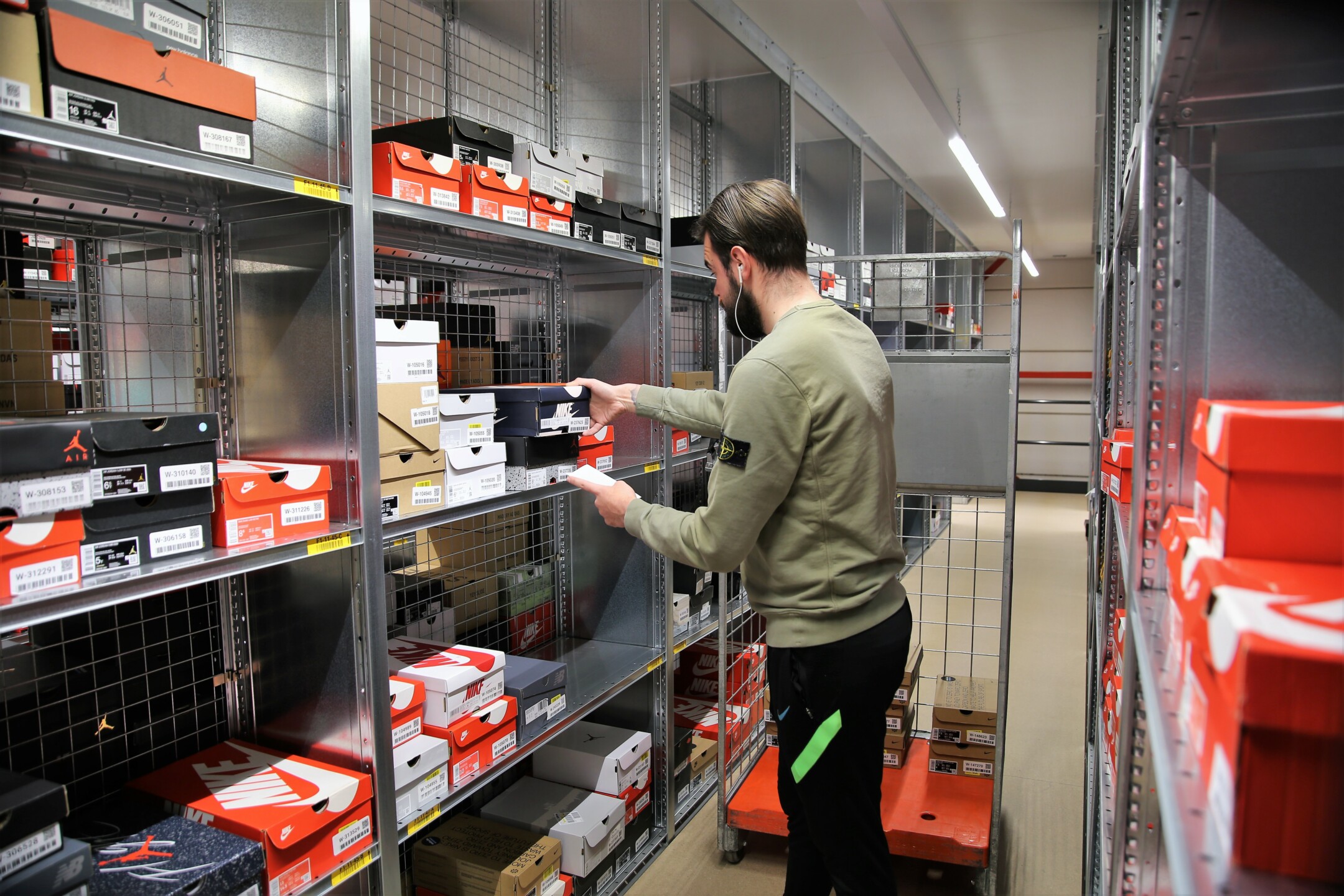
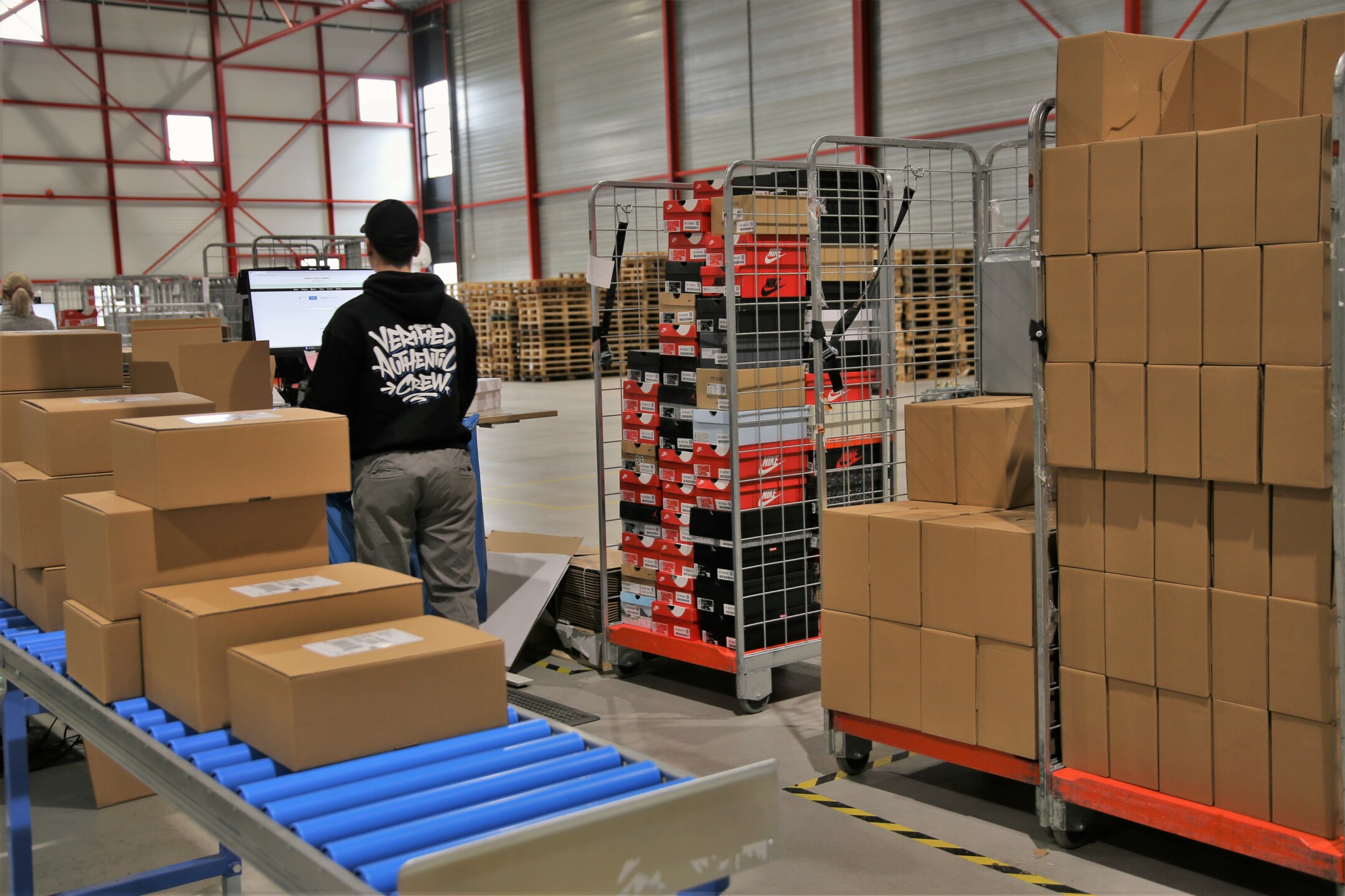
“We even considered the possibility of adding an extra floor, but that’s not a good long-term solution,” states Lopes.
So Restocks decided to separate the operational processes and set up a dedicated facility especially for the consignment operation. The company found a suitable 2,900m2 building in the town of Waalwijk. “It had three dock doors but had not yet been fitted out, so it was perfect for our needs,” recalls Lopes. But setting up a new fulfillment center is a whole new ball game that involves thinking about picking and packing processes, picking routes, zoning, storage systems and more.
Right expertise
“We didn’t have the right in-house expertise for that, so we started looking for a partner who could help,” he says. Restocks decided to make use of Groenewout’s expertise. There was a clear goal: to design both the building and the processes with efficiency in mind.
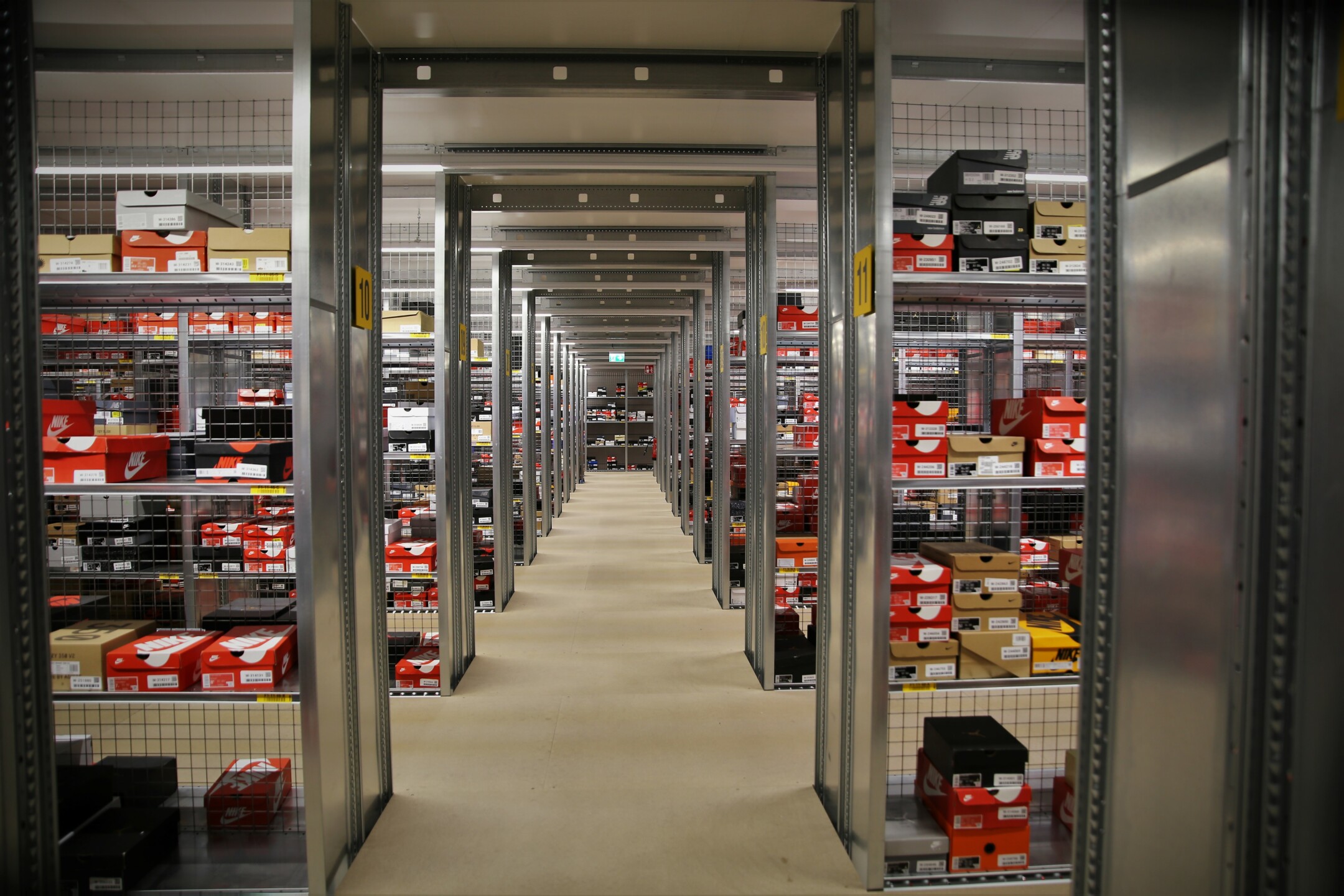
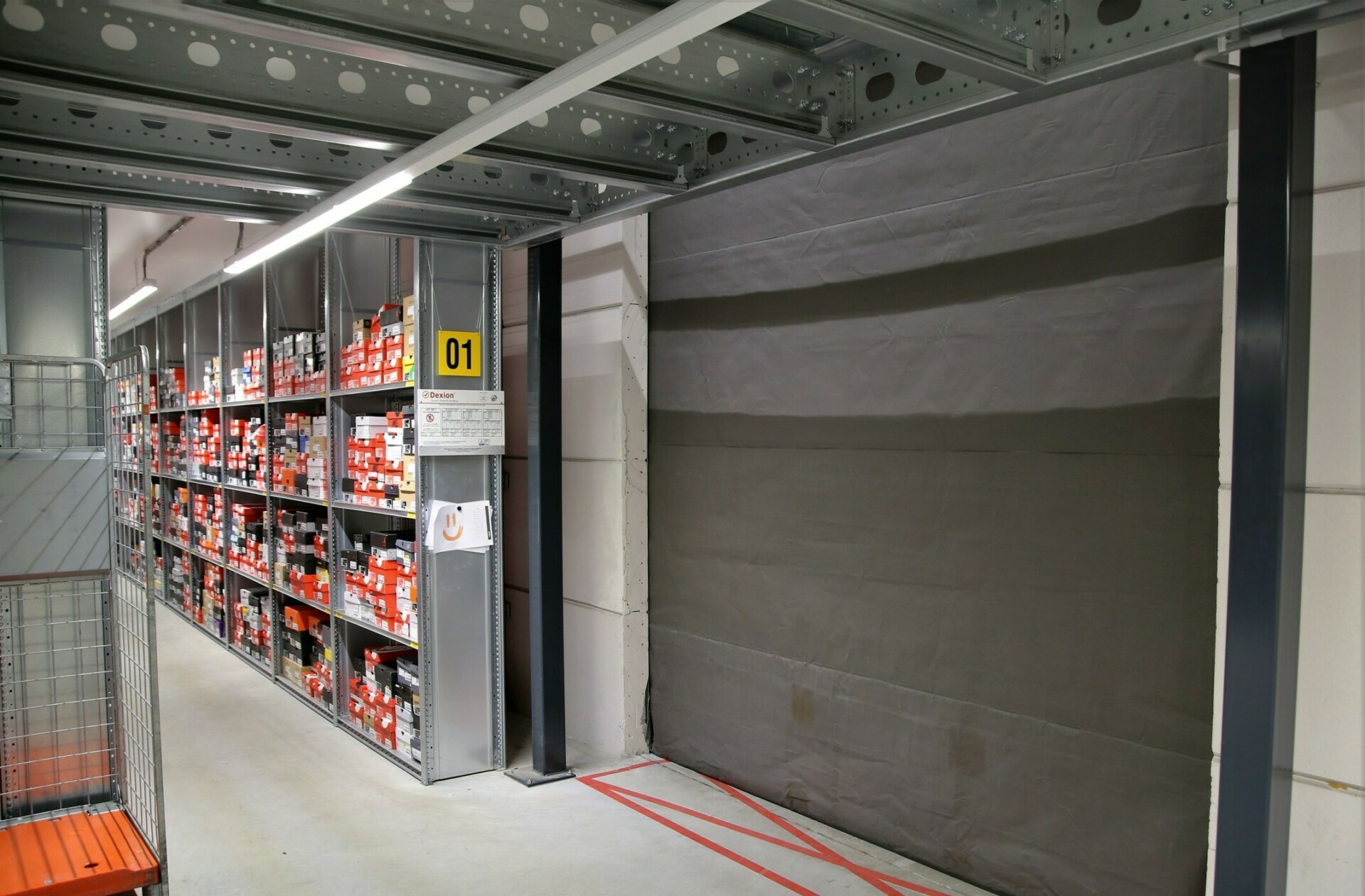
“We discussed our needs and requirements with the Groenewout team, and we also visited a number of their existing clients to gain inspiration,” Lopes continues. Groenewout subsequently took everything off his hands. “The whole process was very pleasant. Communication was fast and easy, and our new fulfillment center was ultimately realized quickly too,” he adds.
Restocks moved into the new building in April 2022, barely seven months after initially meeting with Groenewout. The intelligent positioning of the shelving ensures a high storage density, resulting in space for 200,000 items. The current storage level is 75,000 items, so there is still plenty of growth potential. Restocks currently uses eight workstations for picking and packing, but there are expansion opportunities here too.
Honest advice
“The processes are a lot more efficient than before. We now have four permanent employees working in the fulfillment center,” he explains. Restocks can bring in extra staff from its regular flex pool during peak periods.
The team pick, pack and ship about a thousand orders to clients throughout Europe every day. Lopes is full of praise for Groenewout’s knowledge and advice: “They took a proactive approach to solving our problems and their advice was open and honest – even if that meant that we had to put an investment idea on ice. For example, we seriously thought about installing an automated packaging machine: a sizable expense, but it seemed like a logical option given our growth figures at that time. But when the market weakened and growth suddenly slowed, we decided to listen to Groenewout’s advice and not to invest in such a machine after all. Having said that, we’ve done all the groundwork now, so perhaps we will decide to get one eventually.”
Permits and insurance
Lopes is also extremely satisfied with the help Groenewout provided with permits and insurance. Due to the high value of the stock, the entire exterior wall had to be fitted with three-meter-high steel sheeting and a vibration sensor, and the company had to install fencing, security cameras and a smoke curtain in order to qualify for insurance. “That was perhaps the most time-consuming aspect of all, but even that worked out well in the end. I don’t know if that would have been the case without Groenewout. They are a true partner for us in every way,” he states.
Future plans
“Thanks to the new fulfillment center and current processes, we’re ready for the future,” says Lopes. In fact, behind the scenes, work is already underway to build that future. The Restocks platform has recently been integrated with other platforms, for instance, and it will soon be possible for the fulfillment center to handle different flows of goods. The company is currently in the pilot/test phase as the basis for further optimization measures.
According to Lopes, he might even enlist Groenewout’s knowledge and advice again for that project. “We’ve learned two important lessons: make sure what you do is scalable, and don’t be afraid to outsource things to specialists if you don’t have the necessary in-house expertise. You can’t do everything yourself. We’re stronger together. And the benefits definitely outweigh the extra costs.”
About the author
Mark Dohmen has been working as a journalist in the logistics sector for 25 years. After studying Logistics Management, he worked as an editor at the trade publications Transport+Opslag, Logistiek and Logistiek.nl and was editor-in-chief of Logistiek Totaal and Warehouse Totaal. He is currently working as a freelancer and produces articles and videos for logisticsinside.nl and logisticsinside.eu.
More information
If you would like more information about this project, please contact Alain Beerens at beerens@groenewout.com or via tel. +31 76 533 04 40. For more information about Restocks, go to https://restocks.net.