We are always thinking one step aheadConsulting, Engineering & Optimization in Logistics Networks
How can we help you?
Kekkilä-BVB increases efficiency and flexibility thanks to new warehouse and production location
Interview with Peter Jan Kuiper (COO) and Douwe van Buuren (Head of Maintenance and Investments) at Kekkilä-BVB
With the completion of an entire warehouse, located directly next to the production site in De Lier, and the construction of a modern production facility in Wanssum, Kekkilä-BVB has taken major steps in its continued expansion. Kekkilä-BVB enlisted the expertise of logistics specialist Groenewout for both projects.
BVB are the initials of founder Bas van Buuren, but nowadays BVB Substrates stands for so much more. With over 100 years of experience, BVB Substrates has become a European market leader for professional growers. Today, the brand is one of the professional substrate brands owned by Kekkilä-BVB, Europe’s largest producer of horticultural substrates. Kekkilä-BVB has various production locations in the Netherlands, including in Drachten, Grubbenvorst, Hardenberg, De Lier and Wanssum. The company enlisted the expertise of Groenewout for the latter two locations.
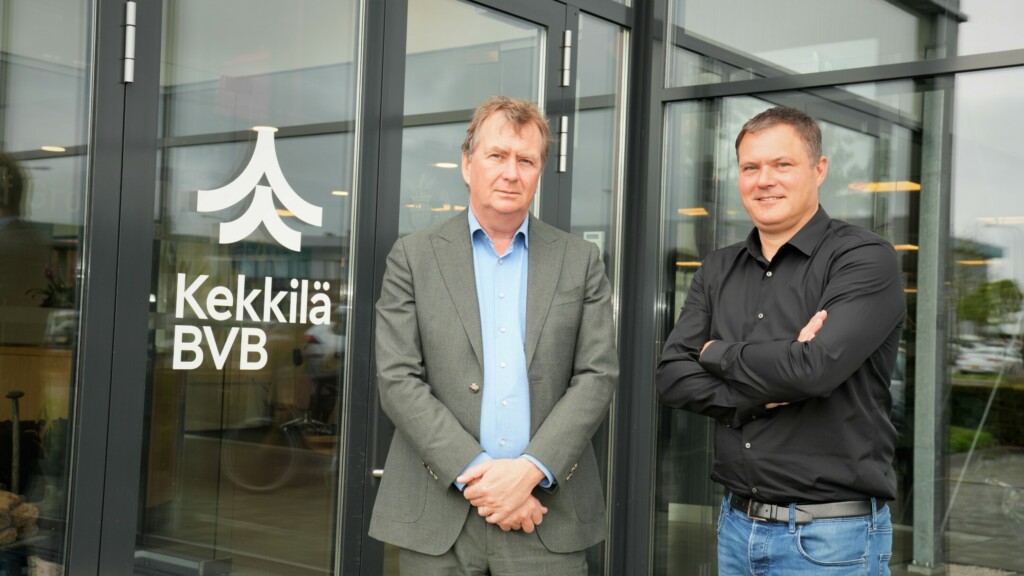
Feasibility study
“We first met Groenewout when we were planning a warehouse in De Lier,” says Peter Jan Kuiper, COO at Kekkilä-BVB. DCM, one of the company’s biggest clients, had asked him to help them think about ways to handle their continued growth. Kuiper: “They wanted to take a cross-docking approach at our production site to combine shipments for delivery to Dutch customers. Naturally, we wanted to help DCM, but the issue was too complex for us. We therefore asked Groenewout to conduct a feasibility study and do the necessary calculations.” The study concluded that it was feasible for the company to build its own 5,500m² warehouse, with space for 10,000 pallets, on the existing site in De Lier.
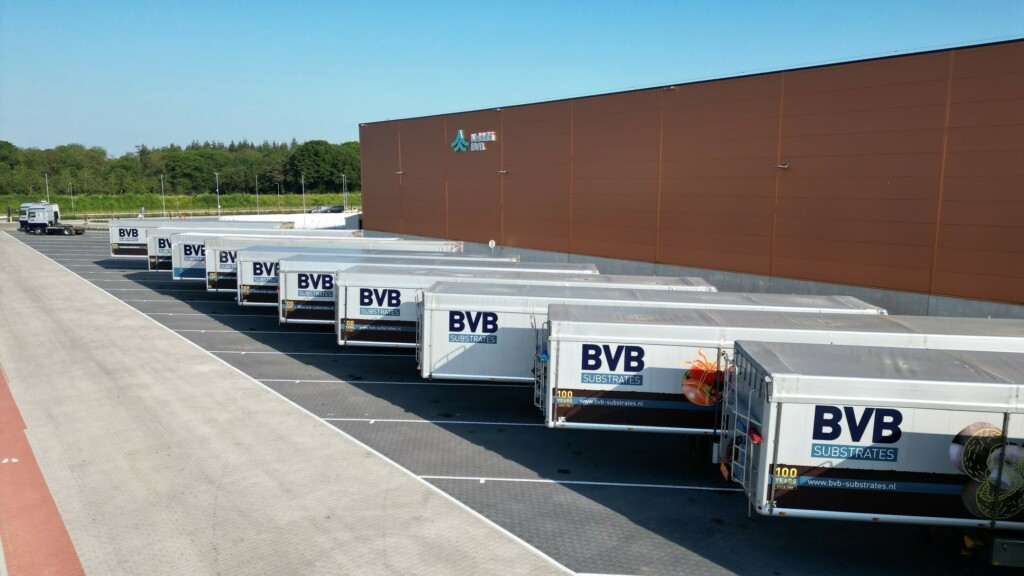

Increased efficiency
“By this time, however, our approach had changed,” adds Douwe van Buuren, Head of Maintenance and Investments at Kekkilä-BVB in the Netherlands. “We had initially wanted to set part of the warehouse aside for DCM, but we eventually chose ─ in consultation with the customer ─ to use the entire warehouse for our own products.”
The building is connected to the production area via a roll conveyor. Pallets travel from production in a continuous flow and are then put away in compact drive-in racks using reach trucks and shuttles. “The studies showed that this is the most efficient setup for our situation,” states Van Buuren.
The warehouse enables the production of larger batches, which is much more efficient, but the new warehouse also created the need for a WMS. “So we asked Groenewout to help us with this,” says Kuiper. “They analyzed our entire organization, including all our logistics processes and document flows, and helped us select the right WMS provider.”
More structure, fewer mistakes
The new building was ready, and the warehouse was operational, in a record time of less than four months. This short construction period was crucial for Kekkilä-BVB due to the seasonal nature of its operations. “We would never have managed this without Groenewout”, states Kuiper. “You need to speak the right language, especially in construction. That can be very tricky if it’s unknown territory for you, so a good partner is essential.”
They are both very satisfied with the result. Van Buuren: “There is absolutely more structure in the entire operation. There is a clearer overview of processes and a minimal chance of error.”
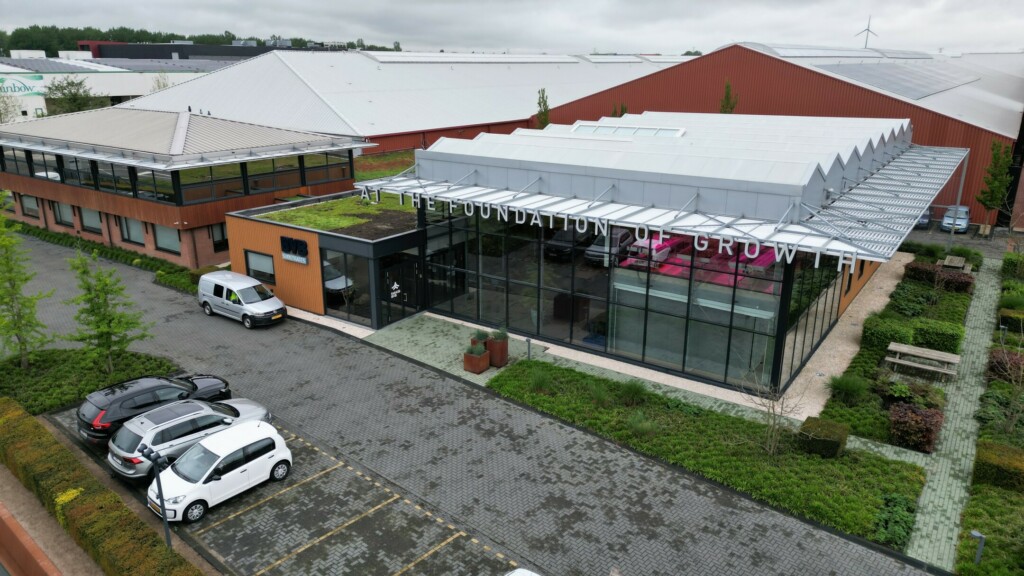
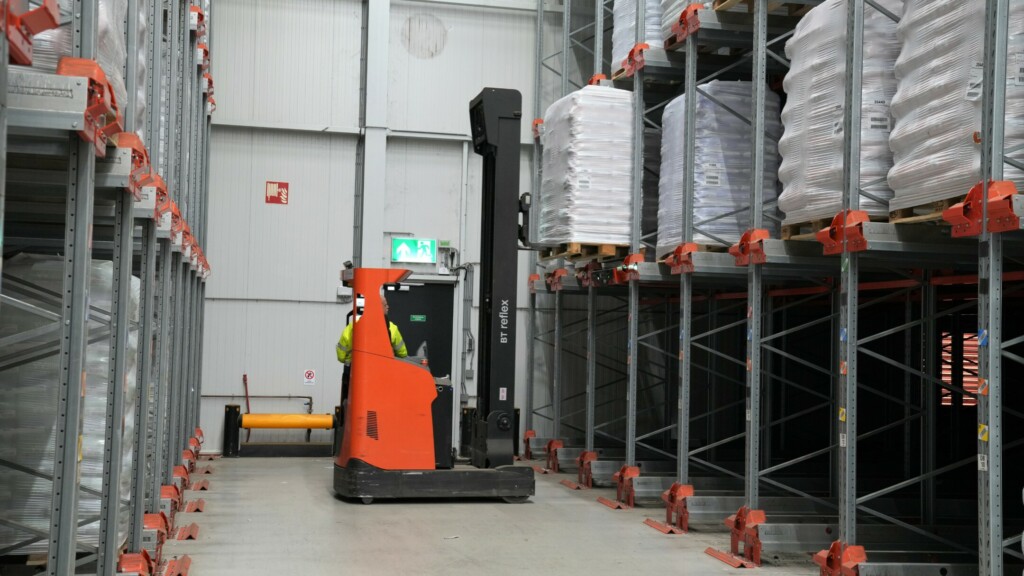
Different mindset
This structure and insight are partly thanks to Sales & Operations Planning (S&OP), which Groenewout introduced and helped the client to optimize. “We now know exactly what we need to do in production. This enables us to improve our procurement and to optimally plan and harmonize the capacities. Based on an annual production of 2.5 million cubic meters in the Netherlands, that adds up to a lot,” observes Kuiper. Van Buuren nods, before saying: “We have shifted from a production peak to a loading peak. But that really required a change in mindset, and Groenewout’s expert help was once again very valuable.”
“The partnership with Groenewout has been incredibly beneficial. There was a click from day one, as their down-to-earth, no-nonsense approach is a perfect fit with our company. They provided indispensable expertise and experience in numerous areas,” continues Kuiper. Van Buuren adds: “What’s more, their advice was very honest. Groenewout truly wants to help the client.”
Various scenarios
In view of the excellent results and satisfaction with the partnership, Kekkilä-BVB subsequently asked Groenewout for advice on the bigger picture for the company in the Netherlands. The consulting firm analyzed all the logistics flows and processes and modeled various scenarios. The study revealed the best location for producing each product. This information came in handy when it was decided to phase out the production of casing soil (for mushroom cultivation) and move it to a new location.
Kuiper: “For years, we had produced casing soil at our site in Grubbenvorst, alongside various retail products. However, an increasing focus on sustainability and tighter requirements have forced us to reduce the proportion of peat and turf in retail products and to work even more hygienically, meaning that we had to search for a new location for our casing soil production.”
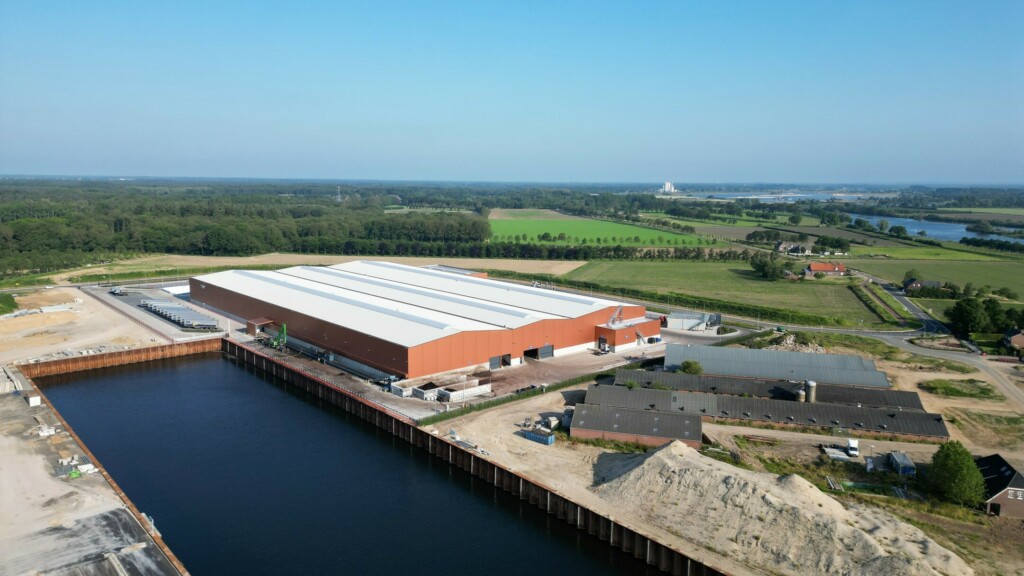
New-build project
The search was far from simple. “It is difficult to find any available land these days, but on top of that we needed to be close to an inland waterway so that we could unload barges carrying bulk raw materials directly onto our own premises,” explains Kuiper. Eventually, a suitable five-hectare greenfield site was found in Wanssum, including its own quay. “Once again, we turned to Groenewout for help with this project,” he recalls. Groenewout coordinated the construction process of the new building in Wanssum, and also took care of the project management, the tender process, supplier selection and implementation of the necessary technical systems. “And those systems were urgently needed,” Van Buuren adds. “The previous systems had been in use for 30 years and it was definitely time for them to be replaced.” With the new technical systems and its own quay ─ where barges are unloaded daily ─ Kekkilä-BVB meets the latest standards, including in terms of sustainability. Furthermore, the move has freed up space for further optimization in Grubbenvorst. “We will be sure to contact Groenewout again next time the need arises,” concludes Kuiper.
About the author
Mark Dohmen has been a journalist in the logistics sector for 25 years. After studying Logistics Management, he worked as an editor for the trade publications Transport+Opslag, Logistiek and Logistiek.nl and was editor-in-chief of Logistiek Totaal and Warehouse Totaal. He is currently working as a freelancer and produces articles and videos for logisticsinside.nl and logisticsinside.eu.
More information
If you would like more information about this project, please contact Groenewout, tel. +31 76 533 04 40. For more information about Kekkilä-BVB, see: www.kekkila-bvb.com