We are always thinking one step aheadConsulting, Engineering & Optimization in Logistics Networks
How can we help you?
Forbo: Productivity increase following successful WMS implementation
An interview with Mr Kees van de Lagemaat, manager logistics, and Mr Urban Deering, manager ICS, from Forbo Flooring in Assendelft, The Netherlands.

In the summer of 2013 Forbo Flooring opened a brand new, 5,500-square-meter distribution center next to its factory in Assendelft. The new DC enables the company to meet the rapidly growing demand for linoleum and luxury vinyl tiles and floor panels. Using the facility to consolidate the flows of goods from its other 11 factories also enables Forbo to save millions of euros each year on logistics costs. An operation of that kind demands an intelligent warehouse management system (WMS), but Forbo did not have one. “We had an ERP system, but that didn’t provide sufficient warehouse management support. It lacked the necessary ‘intelligence’ to manage our processes smartly,” says Kees van de Lagemaat, manager logistics.
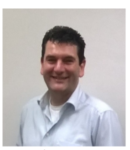
Therefore, Forbo decided to develop its own new warehouse management system just as it had done previously for another warehouse. “We were happy with the result of that exercise – it was a user-friendly system with a fairly simple set-up that was easy to tailor to our needs,” states Van de Lagemaat. His colleague Urban Deering, manager ICS, adds: “Of course there are good standard warehouse management systems on the market, but they dictate the working methods to be used. By developing a system ourselves, we could continue to work in our existing manner.”
ERP system first
During the construction of the distribution center, it became clear that the new building would be completed three months ahead of schedule. Since it would not be possible to implement a fully functional WMS within that time frame, it was decided to uncouple it from the project and open the DC without it. Hence, Forbo quickly enlisted the help of Groenewout, which had previously coordinated the entire new-build project for the DC. “Groenewout knows us well and knows how we operate.
Plus we were very satisfied with our earlier collaboration,” explains Van de Lagemaat. Heeding Groenewout’s advice, Forbo first decided to backtrack slightly and to use the existing ERP system instead. That created some breathing space in order to take a thorough look at the new WMS. That evaluation revealed that not all the functionalities had been sufficiently thought through. “When implementing a new WMS and integrating it with the ERP system, it’s important to decide which tasks will be handled by which system. For example, will the goods-received check be done in SAP, where all the purchase orders are, or in the WMS which manages the operational processes in the warehouse? We hadn’t defined that clearly enough,” says Deering by way of illustration.
Renewed trust in the WMS
Forbo and Groenewout tackled the WMS project again step by step. The functional design has been largely reworked, benefiting greatly from Groenewout’s knowledge of best practices. “Needless to say, our choice to develop our own WMS was also reassessed. We explored whether we could develop the required WMS functionality in SAP, for example, but that would have taken us a lot longer,” explains Deering.
In order to exclude every possible risk, Forbo paid extensive attention to compiling the work instructions in the months before implementation, and to testing scenarios by involving key users who were relieved of their day-to-day duties especially for that purpose. “That was a key phase for us, in which we really got to know the system well. Plus we discovered 180 errors during testing which we were able to resolve before going live. That helped to ensure that everyone has gained renewed trust in the system, despite the delay,” says Van de Lagemaat.
The WMS went online in the spring of 2014, eight months after the distribution center had originally opened, without any noteworthy problems. Van de Lagemaat: “Of course there are always a few minor teething problems following implementation but they were solved quickly. We saw an increase in productivity after just two weeks.”
A fresh pair of eyes
Both Van de Lagemaat and Deering agree that Groenewout played an important role in the success of the implementation. “The consultant from Groenewout ensured that everyone was in agreement about how the functionalities should be set up and that everyone understood what was going to be developed. That was a pretty challenging task, not least because a lot of people within Forbo had become skeptical after the postponed implementation. There was a lot of negative energy but Groenewout dealt with it well,” says Van de Lagemaat.
“Sometimes a fresh pair of eyes is needed,” adds Deering. “Groenewout has demonstrated that it has lots of experience with projects of this kind. The consultant was there from start to finish, even during the actual implementation process, despite that meaning long days. We all really appreciated that.”
Since then, Forbo has enlisted Groenewout’s help yet again, this time to supervise the second phase of the WMS implementation. “Time pressure meant that we were unable to develop all the functionalities in the first phase. In particular, we left the support for reverse logistics until later. Moreover we’re now six months down the line and many new needs have since emerged which can contribute to further process improvements,” says Van de Lagemaat, who adds that he is happy to have Groenewout involved in the process: “Groenewout is aware of the common pitfalls and helps to ensure that we avoid them.”
By Marcel te Lindert
Marcel te Lindert is a journalist with over 20 years of experience in logistics. He was editor-in-chief of the Dutch magazines Transport+Opslag and Logistiek. Today he works freelance for magazines like Supply Chain Magazine and Logistiek Totaal.
More information
If you have questions or if you would like to offer your feedback on this article, you can contact Isabel Schouten-van Dilst, schouten@groenewout.com /+3176 533 04 40.